Date: March 11, 2024
Designer: Caleb Mueller
Objectives and Constraints
- Objective: Create a 3D printed polycarbonate actuator, modeled from a broken piece
- Constraints: Must fit a press-fit metal bearing from the original
Materials and Tools
- Software: Autodesk Fusion
- Materials: Polycarbonate filament
- Equipment: Bambu Lab X1C 3D printer and digital calipers
Phases of Development
I. Measurement
- The broken piece was temporarily glued back together and measured using calipers, then profile pictures were taken for reference.
II. CAD Modelling and Prototyping
- The actuator was modeled in Fusion using measurements and profile pictures as canvases for the more complex shapes.
III. Printing of Final Products
- The model was printed using PC filament and supports on a Bambu Lab X1-Carbon 3D printer. The original metal bearing was press fit into the replicated actuator.
Skills Developed
- Modeling of a complex shape using canvases
- 3D printing of a complex shape with support structures
- Tolerances for press-fit metal
Support and Resources
- Client Sydney Philpott provided photos of the finished product in use on the record player/turntable
Product Images
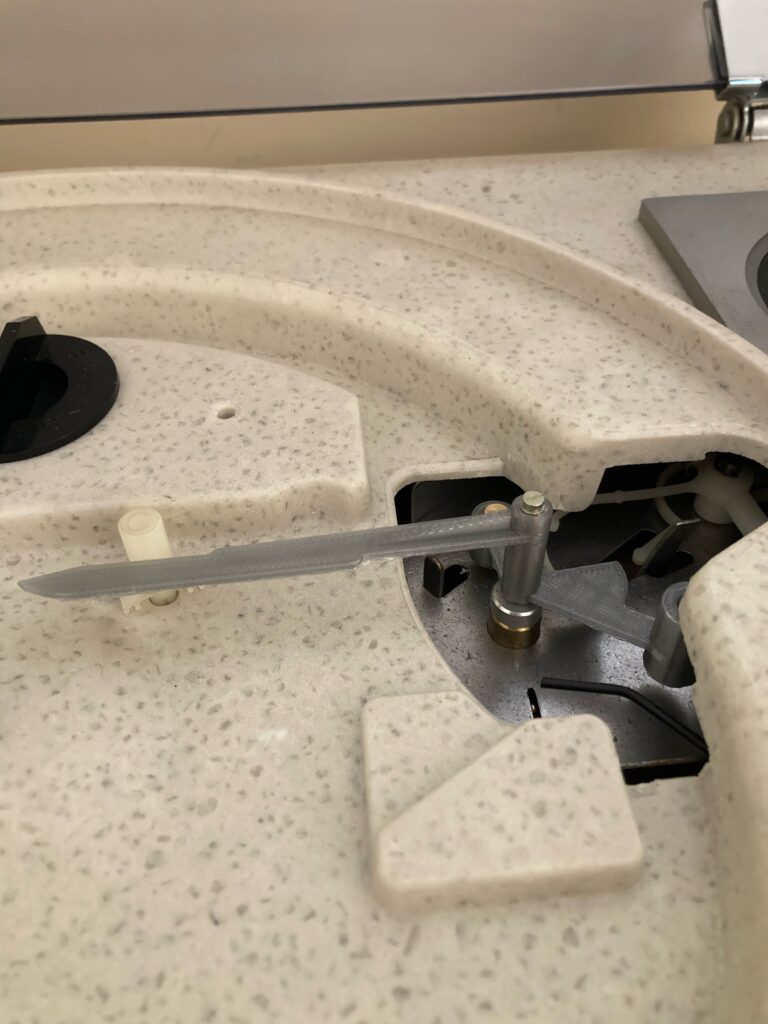
- Figure 1: 3D printed actuator in-use on the record player/turntable
Client Feedback
“The piece fit well into the record player, and it moves the record player arm like the old broken piece was meant to do!”
- Sydney Philpott